Tech News
It is fairly easy to solder or sweat copper pipe. After reading this blog and with a little practice you should be able to do repairs or improvements to your bathroom easily. This blog is useful for those who have read the blog 'How to change a vanity faucet' and would like to add a valve or threaded end for the water lines to attach to or those interested in sweating copper for indoor water lines.
The basic idea of sweating copper is the join or weld two pieces of copper piping together. This can be an very easy task or it can be a nightmare. Preparation is all the difference. If the pieces you are fitting are clean and dry it should be easy. If they are dirty then the solder won't stick and if water is in the pipes it won't get hot enough.
If you are not planning on doing much copper soldering then you are probably better off buy a compression fitting or Shark Bite fitting instead of the tools. Compression fitting are attached by tightening a bolt onto the valve or fitting and the water seal is created by the ring that is compressed between the bolt and the fitting. All you really need are two wrenches to tighten the fitting but it requires a fair bit of strength. Shark bite is a name brand of fittings that just slide on and are called push fittings. These alternatives are more expensive than soldered fittings but not if you have to buy the tools for a one time use. If you are doing or planning to do a lot of plumbing then it is cheaper to go with the solder fittings.
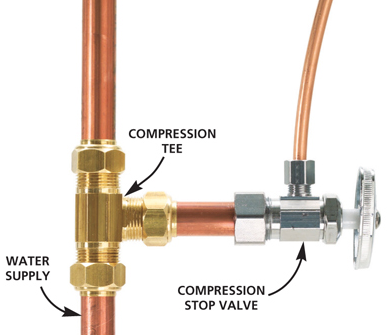
You will need:
Remember: