Hot Forging And Casting
Brass Forged/Hot Forged/Cold Forged Components
Forging is a manufacturing process during which presses, hammers, and dies are used to force metals into various shapes. Forging can be done at room temperature (cold forging) or metal temperatures of over 1000 degrees Celsius (hot forging). The forged parts can weigh from a few ounces to hundreds of tons.
US $0.05 - 0.25 / Piece
Price:US $0.05 - 0.25 / PieceProduct Details
Brass Forged/Hot Forged/Cold Forged/ Forging Components
Forging is a manufacturing process during which presses, hammers, and dies are used to force metals into various shapes. Forging can be done at room temperature (cold forging) or metal temperatures of over 1000 degrees Celsius (hot forging). The forged parts can weigh from a few ounces to hundreds of tons.
Brass Forged/Hot Forged/Cold Forged/ Forging Components
The Art of Forging
While the earliest signs of metalworking date back to Mesopotamia around 4500 B.C., the art of forging flourished between the 10th and 12th centuries A.D. It was during this period that the Romans discovered that water, and the power that it was capable of generating, could be used to operate bellows and hammers.
The steam engine of the 19th century ushered in the era of modern forging. Electrical power and the development of explosive forming soon followed. At its earliest stages, forging produced decorative objects from precious metals. Today, it’s a global process with many applications in every industry.
Why Use Forgings?
Forgings provide uniformity of composition and structure. The thermal cycle and deformation process result in metallurgical recrystallization and grain refinement. In other words, it produces a steel product that is incredibly durable and impact-resistant.
Forged steel is stronger and more reliable than plate steel because its grain flows have been altered and conform to the shape of the part.
Brass Forged/Hot Forged/Cold Forged/ Forging Components
OEM TS16949 hot drop die close crankshaft forging parts/forging
The advantages to using a forging include:
- The tight grain structure of a forging makes it mechanically reliable while offering superior wear resistance
- There are no porosity, cavities, or shrinkage
- It’s tougher than the alternatives
- It’s excellent at handling impact
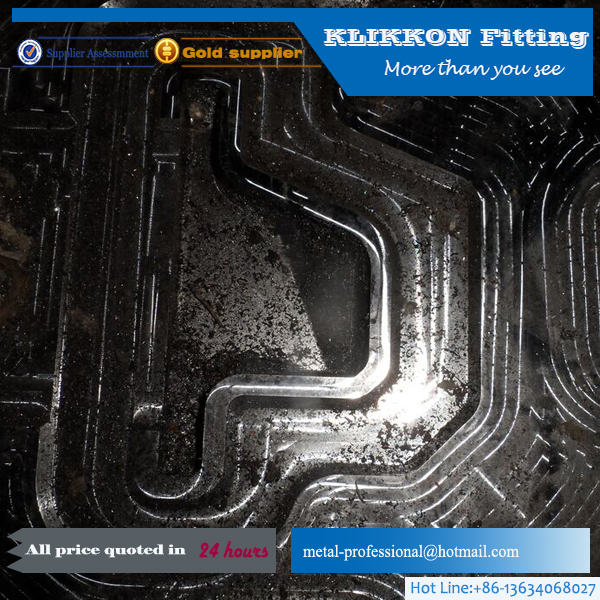
How Do Forgings Differ from Castings?
While forging is applying thermal and mechanical energy to solid steel ingots or billets, castings are produced by pouring molten metal into a mold that has been made to the desired shape.
Parts that are too intricate or large for the forging process are often cast. The tooling (patterns and core boxes) that is used to produce castings is less expensive than forging dies. Depending on how the part will be used, however, the strength and reliability of forgings make it the better choice.
How are Forged Components Used?
Forged parts are appropriate for almost any industry. Here are just some of those industries and a list of components made from forgings:
- Automotive: When it comes to cars and trucks, you’ll find forged parts at the points of stress and shock such as steering arms, axle shafts, torsion bars, and kingpins. They are also used in the powertrain where connecting rods, drive shafts, universal joints, and differential gears are all forged.
- Aerospace: Forgings are frequently used in helicopters, spacecraft, military aircraft, and commercial jets because of their structural reliability. They are ideal for parts that require a variety of sizes and shapes such as bulkheads, hinges, engine mounts, shafts, wheels, brackets, and landing gear cylinders. In jet turbine engines, super alloys are forged into components such as discs, blades, couplings, manifolds, rings, chambers, and shafts.
- Ordnance: You will find forged components in tanks, armored personnel carriers, and heavy artillery. They are also used in rifle triggers, missiles, shells, and the drive shafts in nuclear submarines.
- Agriculture: Farm implements need to be strong and sturdy. Components that are subjected to impact and fatigue—gears, shafts, levers, and spindles—are manufactured from forgings,
- Oil Fields: Forgings are the choice for rock cutter bits, drilling hardware, and high-pressure valves and fittings.
- Construction: It stands to reason that components for the construction and mining industries would require toughness and strength. Forgings are used here for sprockets, ball joints, yokes, axle beams, gears, and all kinds of shafts.
- Hand Tools: Ball-peen hammers, pliers, sledge hammers, wrenches, and garden tools, as well as surgical and dental instruments, are examples of forged hand tools.
A Critical Part of the Process: The Forging Die
Some forgings are simply round or rectangular blocks. Others have the finished shape of the final component. The latter forgings need to have a manufactured die to create the shape. In a procedure called closed-die forging, the metal is placed on the die and pressed or hammered so that the metal forms into the die and copies its shape.
Not just any machine shop can make forging dies. It requires the experience and expertise that only comes from years of working as a tool-and-die shop. The dies must be precisely machined and carefully heat-treated to shape the workpiece correctly, as well as to withstand the tremendous forces involved in most forging operations.
Metal prototyping, machining, and forging are interrelated. Initially, metal-forming dies for forged parts are precision machined and heat treated. Then, forged parts may be machined for further finishing.
Klikkon offers die-making services to provide manufacturers with more options for making parts with high strength. Our factories are ISO 9001 compliant and can provide you with quality dies produced on three, five, and seven-axis CNC machines. To streamline your operations, we can also machine your parts to your preferred finish. We work with you to meet your specs, budget and deadlines.
Ask us for a quote. You’ll find that accurately machined dies are not beyond your budget.
Request a free consultation and receive 20% off your first order.